World-renowned guitars are arranged at a guitar clinic with a Unior tool developed specifically for the occasion
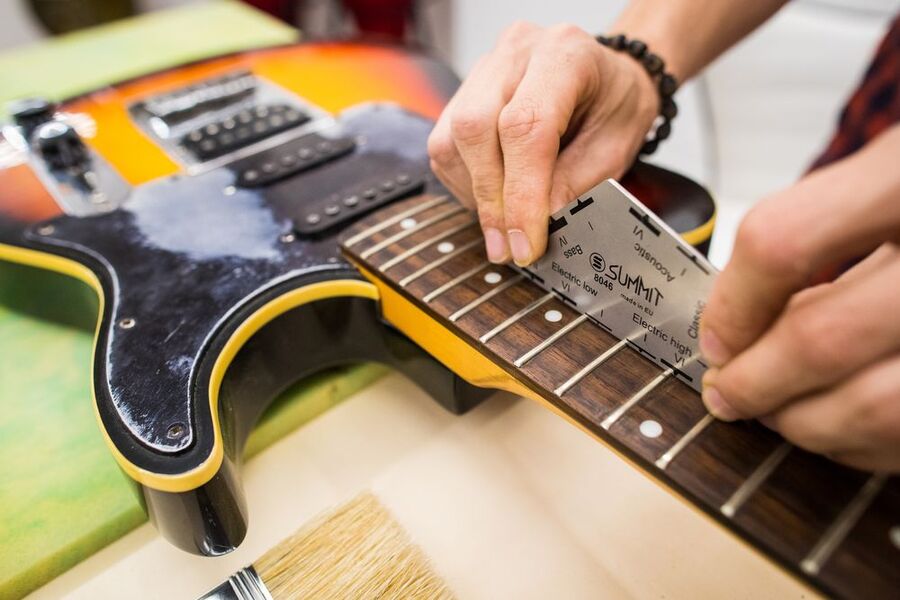
A guitar is considered one of the most recognizable instruments among musicians, and its worldwide sales value amounts to millions. Guitars are most widespread in the US, where between 600 and 700 million guitars are sold annually, while Spain, which is considered the cradle of guitar, produces as many as 800,000 acoustic guitars annually. The very top of the world's "guitar fairy tale" is being co-created by a Slovenian, Davorin Sever, a guitar manufacturer well-known to many local and worldwide stars and guitar lovers around the globe. What is a mystery to many? At his so-called "guitar clinic", Davorin repairs, services and manufactures guitars using Unior tools, designed specifically for the occasion.
Nowadays, Davorin Sever is establishing workshops or the so-called "guitar clinics" all over the world. Not only in Slovenia, specifically in Izola, but also in China, Italy, Spain, Great Britain and elsewhere. Through his 40 years of experience, countless hours of practice and hard work, he came to the awareness that in this world, one must simply be the best, and what counts the most is the quality and attitude towards the instrument, the material and, last but not least, towards the owner. At the same time, great emphasis is put on speed and price. However, all great things take their time, and he is keenly aware that being different and unique is of great importance. It is becoming increasingly clear that people no longer want copies of selected guitars owned by world-renowned musicians, but rather seek something of their own, something with a personal touch. Nevertheless, Davorin emphasizes the following:
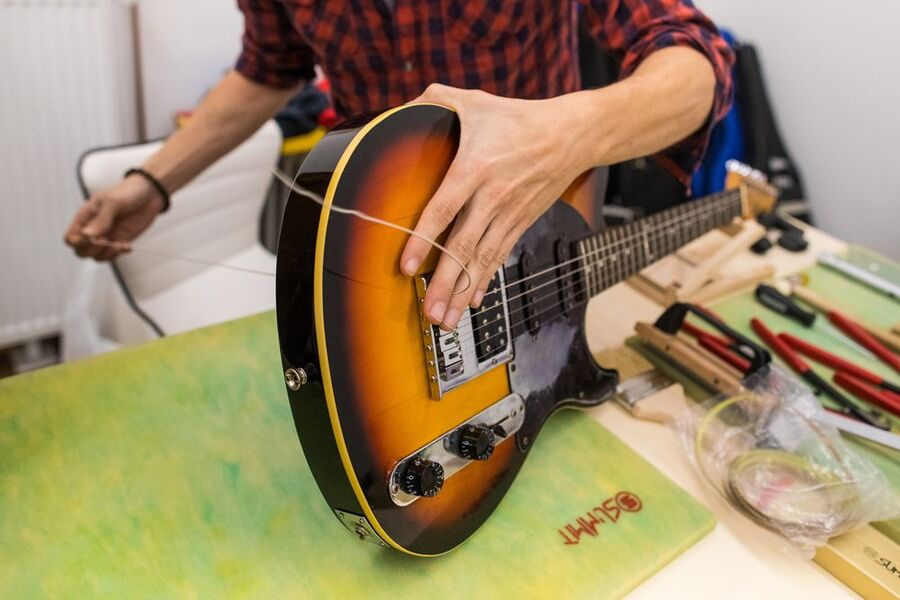
"It all starts with wood, which determines the tone color and responsiveness. The most commonly used wood is maple. It is best to combine different types of wood as they have different tonal properties. The selection is made according to the desired sound. People are usually not familiar with the importance of specific details. If the guitar neck is light in color, the sound is brighter as well. Spruce turns out to be a very good wood for electric guitars as it has the fastest sound transmission, 5,900 meters per second. The most interesting shapes of guitars we created include guitars in the shape of a car, a locomotive, U2; many things can be done. The most important thing is the ''raw'' guitar sound. The way the wood is glued is of utmost importance as it must "rest" afterwards. The guitar should be free of any internal tension. Nowadays, guitars are glued at the factories and further processed the very next day, which does not work as the proper making of a guitar takes time. It also makes it more durable; it can practically last forever as it is less susceptible to external influences."
Guitar clinic enriched with Unior tools
At the guitar clinic, each guitar is carefully inspected. Most often the frets are replaced, as they are the easiest to wear out, and as such they directly affect the sound, intonation disturbances and the buzzing of the strings. It is for this reason, and with a view to achieve the desired quality and meet all the needs and desires of his customers, that Davorin has developed a very special hand tool in cooperation with Unior:
''We have a unique process using a special tool that we have developed ourselves and which is being marketed worldwide. I have my very own concept that is no secret. If the manufacturing process is accurate and the elements, neck and body are fitted, the loss of vibration transmission is minimised. The type of wood and the flow of the wood lines are crucial for the stability of the neck, which must bend as little as possible. It is important to let it settle down - glue, process and leave to rest. Therefore, the making of a new guitar takes up to half a year. Certain special guitars take up to two years to make, which, naturally, is not cheap."
Most of the guitars that arrive at the guitar clinic are neglected, as the owners do not observe the spring-summer or autumn-winter regime. The guitar and the wood in it react differently to humidity, high and low temperatures, since the wood is always alive, hydroscopic, sensitive to moisture or heat. With acoustic guitars, for example, the bridge to which the strings are attached tends to fall off. Cold and moisture damage the neck and cause it to get loose, twisted or bent or the layer of lacquer cracks, and if the air is dry during the heating season, the wood shrinks.
"It's all about rock and roll, and sometimes I jokingly tell people who bring a very neglected instrument that pest control is charged separately. One may see a lot, from moss to algae, and such scenes are truly not particularly eye-pleasing. But sometimes a guitar obviously needs to be tested for how much it can handle," explains Sever.
Whether preserved or neglected, the guitar is a thing of the soul. Playing the guitar should fill us with joy and serve as a relaxation activity. The guitar is a working tool for musicians used to create beautiful melodies and nice sounds for their listeners. This is why choosing a tool to repair such an instrument is not only crucial, but requires a great deal of care and quality and calls for a professional approach. The Unior company considers it a great honour and privilege to cooperate with Davorin Sever and offer hand tools that are used to repair many world-renowned and well-known guitars. The development of further guitar repair tools will thus pose a new challenge in 2020, all with the aim of creating top-notch tunes and satisfying customers at the "guitar clinic" both home and around the world.