Forjado en frío
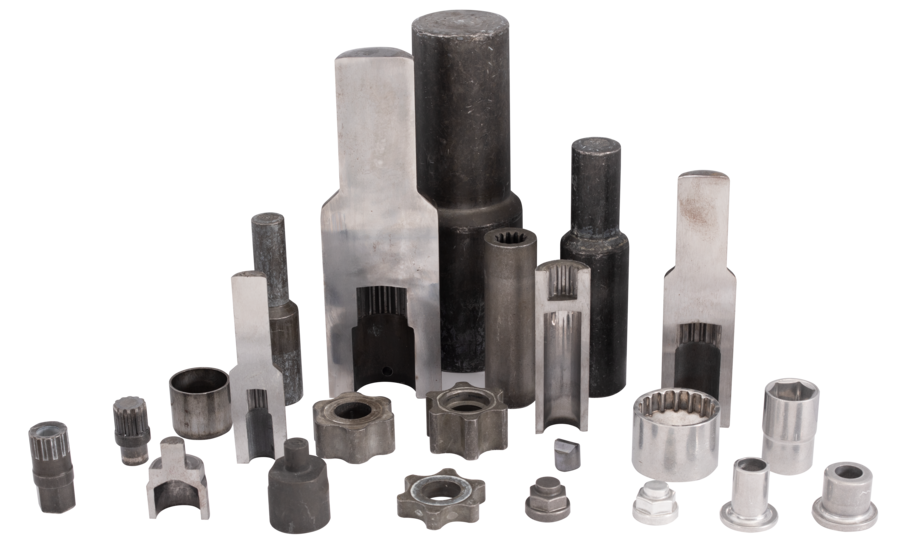
Cold forging, also called cold forming is a process that takes place near room temperature. It’s done by placing the workpiece in-between two dies, and pressing the dies until the metal assumes their shape.
Cold forged parts are produced by using mechanical or hydraulic presses, or automated multi-station cold forming machines where the pre-formed part is transferred from one tool station to the next at high speed with each station performing a specific cold forming process
Cold forging is a reliable and cost efficient process and it is used to produce parts of superior mechanical properties without (or minimum) wasted material. Cold forging can be very efficient for mass production.
Cold forging can be used for shaping different types of material. We offer product from various types of high carbon steel alloys to softer metals like aluminum.
ADVANTAGES OF COLD FORGING
-
savings in material and final machining
-
high productivity
-
excellent dimensional accuracy and surface quality of cold forged parts
-
improvement of mechanical properties of cold forged parts
AREAS OF USE OF COLD FORGED PARTS
-
Water pumps
-
Hydraulic industry
-
Pneumatic industry
-
Agricultural machines (tractors, tractor attachments, working machines)
-
Industry of heavy construction machinery
-
Internal combustion engines (nautical, cargo, automotive, etc.)
-
Automotive industry
-
Bicycle components
-
Motorbike components
-
Military industry
-
Oil/Gas industry
MATERIALS FOR COLD FORGING (STEEL)
-
Steel for carburization ( C10, Ck10, C15,Ck15,16MnCrS5, 20CrMo5, 18CrNiMo7-6, ...)
-
Steel for heat treatment ( CK22, C35, C40, C45, ...)
-
Alloy steel for heat treatment ( 25CrMo4, 34CrMo4, 42CrMo4, ...)
MATERIALS FOR COLD FORGING (ALUMINUM)
-
Pure aluminum (1080A,1070A,1050A….)
-
Hardenable alloys ( 5005A,5754,5056A…)
-
Non age-hardenable alloys (6060, 6082,7075…)