We are delighted to present the new product group, Lean Manufacturing system (LMS)
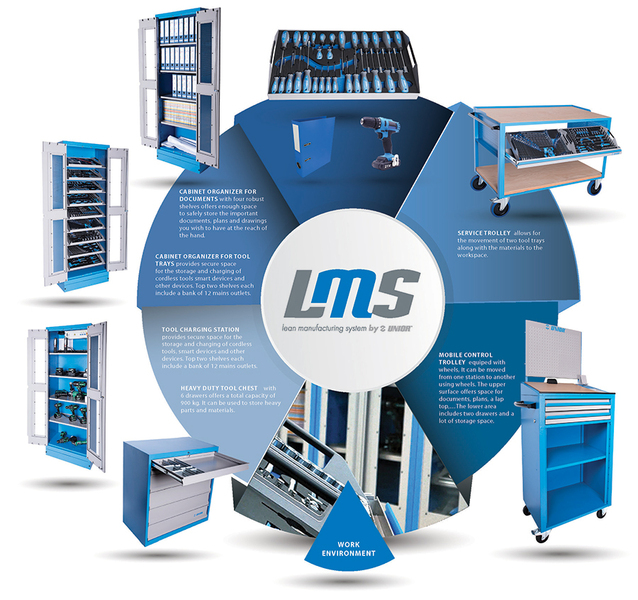
Unior’s Lean Manufacturing System is a line of products optimizing the working process and maintains an orderly working environment. The standardized system is designed regarding the requirements of a lean production line: storage, charging, transport and usage of tools, parts, documents and materials.
The LMS is based on the so called 5S principles, rapidly emerging as an industrial standard for minimizing the loss of efficiency caused by a disorderly working environment.
5S is an acronym of five Japanese words: (seiri - separate, seiton - organise, seiso - clean, seiketsu - standardize, shitsuke - sustained usage). Unior has developed the Lean Manufacturing System using the 5S principles to create a structured, optimized workflow that ensures well-ordered and clean working environment, without losses or bottlenecks.
The main advantage of LMS is a logically connected circular system of products, which you can find in attached presentation. It can easily be applied through all industries, although for now it is most commonly applied to industries with complex production lines and large workspaces, where the LMS allows the allocation of specific tools or other work equipment to each worker separately, thus optimizing the workplace. It also eliminates unnecessary time loss while moving from one work station to another, during the performance of work and generates savings during preparatory work throughout the entire production and purchasing process.