Wrenches
Manufacturing procedure for a combination wrench at Unior
Cutting
Cutting material is the first operation in the technological procedure of wrench manufacturing. Optimum design of a cut provides optimal use of material.

Forging
Forging technology at Unior ensures excellent strength characteristics of wrenches. Notably, it maintains appropriate fiber orientation in a forged part, leaving it uninterrupted and the same as in a rolled blank. That characteristic of forged parts is vital for achieving the characteristics of products exposed to heavy dynamic loads, such as Unior wrenches.
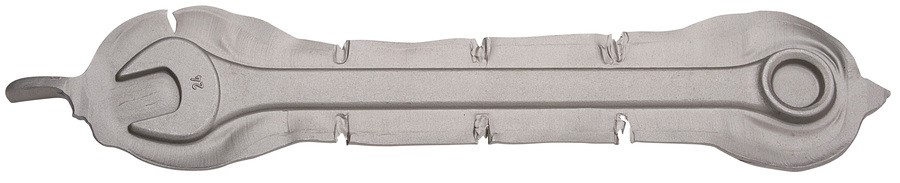
Trimming
Superfluous material around a forged part is removed using a special-purpose trimming tool; material is trimmed to the desired shape, always making the weight of trimmings as low as possible.


Perforation
following the forging and trimming phases, perforations are made in the workpiece by punching or cutting. This procedure can be carried out either on hot or cold workpieces.

Burring and grinding
Wrenches are contour-ground on grinding machines, thus making surfaces smooth on the edges of a wrench. After that, edges on forged parts are made smooth in special machines using mechanical and chemical means.
Machine marking and bending:
Each wrench is impressed with an appropriate marking providing information about the source of a wrench, dimensions and material used. The ring of the wrench is accordingly offset in line with the standard.

Broaching
In broaching, suitable gaps are made on special-purpose tools; material is broached with linear motion of a tool incorporating a large number of cutting blades.

Tempering
tempering by heating and cooling is designed to improve the grain flow of the steel and thereby increase the toughness of the wrench at the desired points; this heat treatment process grants the Unior wrenches a long lifespan and resistance to high loads and pressure.
Sanding
various abrasive substances are blasted onto the surface of the wrenches by means of compressed air. The abrasives burr the surface, while at the same time imparting to it a certain asperity, important for the subsequent application of a suitable galvanic (protective) coating.

Chroming
Wrenches are coated with a thin, but solid layer of chromium oxide to protect them from corrosion and other external influence. Chromium coating gives a wrench a professional appearance and warrants a long service life.
