Sockets with accessories
A special procedure for the manufacture of ratchets
RATCHET
Cutting
Cutting material is the first operation in the technological procedure to manufacture a ratchet casing. Optimum design of a cut provides optimal use of material.
Forging
The forging technology at Unior ensures excellent strength properties of wrenches. Notably, it maintains an appropriate course of fibres in a forged part, leaving them uninterrupted and the same as in a rolled blank. That characteristic is vital for achieving the characteristics of products typically exposed to heavy and dynamic loads, such as a ratchet.
Trimming
Superfluous material around a forged part is removed using a special-purpose trimming tool; material is trimmed to the desired shape, always making the weight of trimmings as low as possible.
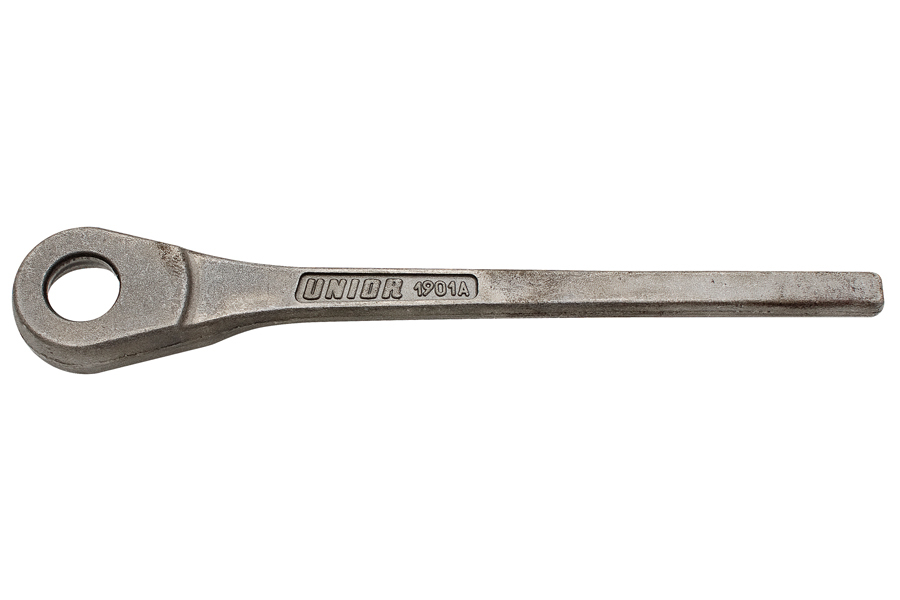
CNC working
A CNC machine is used to make a ratchet casing within the necessary tolerance margins for optimal functioning of the final product.
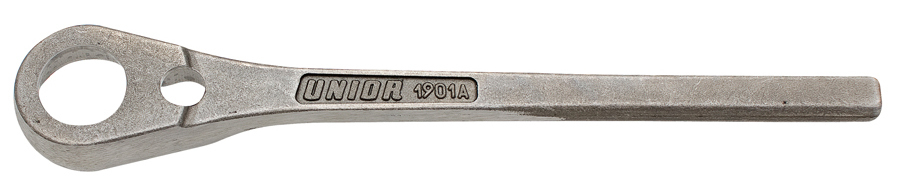
Heat treatment (quenching and tempering)
the heat treatment with hardening and tempering is intended to improve the structure of the steel, to provide greater hardness and toughness of the product and other properties required to overcome the strain that work with such products requires.
Sanding
A ratchet housing is plated with a thin, but hard coating of chromium oxide that protects against corrosion and wear and other external influence. At the same time, it gives the entire product a brilliant and professional appearance.
Chroming
A ratchet housing is plated with a thin, but hard coating of chromium oxide that protects against corrosion and wear and other external influence. At the same time, it gives the entire product a brilliant and professional appearance.
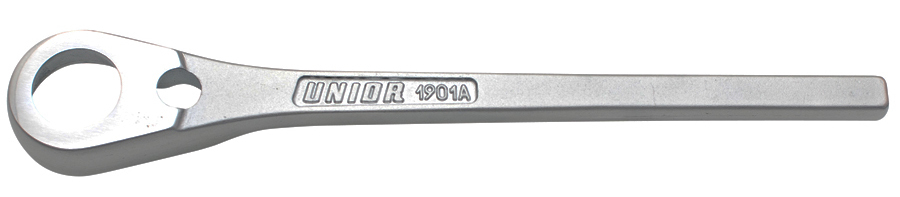
PINION
CNC working
Machining is carried out on a CNC machine, which ensures the necessary accuracy. The pinion is one of the essential elements of a ratchet and individual sizes have to be executed within very narrow tolerance margins.
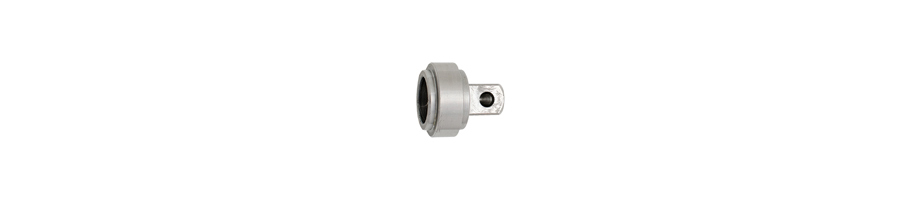
Broaching the serration
Teeth on a pinion are shaped with a broaching operation. The obtained 72-teeth geometry guarantees the necessary two-sided shifting of an Unior ratchet.

Heat treatment (quenching and tempering)
the heat treatment with hardening and tempering is intended to improve the structure of the steel, to provide greater hardness and toughness of the product and other properties required to overcome the strain that work with such products requires.
Sanding
Cleaning the surface after heat treatment.
Shift lever
Closing element
Shift button
Cover
Ejector pin
Ratchet parts 12-16 are made using advanced manufacturing procedures, such as sintering and injection moulding. Quality materials provide optimum strength and premium durability.

Assembly

Final assembly
Well qualified, skilled and meticulous employees performing the final ratchet assembly will assemble the product into a whole ensuring a top-quality final product. An Unior ratchet will withstand up to 30% higher loads than standard requirements.
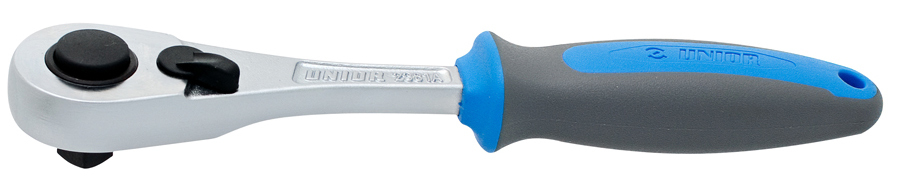