Pullers
A special procedure for the manufacture of pullers
Head (body)
Cutting
Cutting material is the first operation in the technological procedure of wrench manufacturing. Optimum design of a cut provides optimal use of material.
Forging
Forging technology at Unior ensures excellent strength characteristics of wrenches. Notably, it maintains appropriate fiber orientation in a forged part, leaving it uninterrupted and the same as in a rolled blank. That characteristic of forged parts is vital for achieving the characteristics of products exposed to heavy and dynamic loads.
Trimming
Superfluous material around a forged part is removed using a special-purpose trimming tool; material is trimmed to the desired shape, always making the weight of trimmings as low as possible.
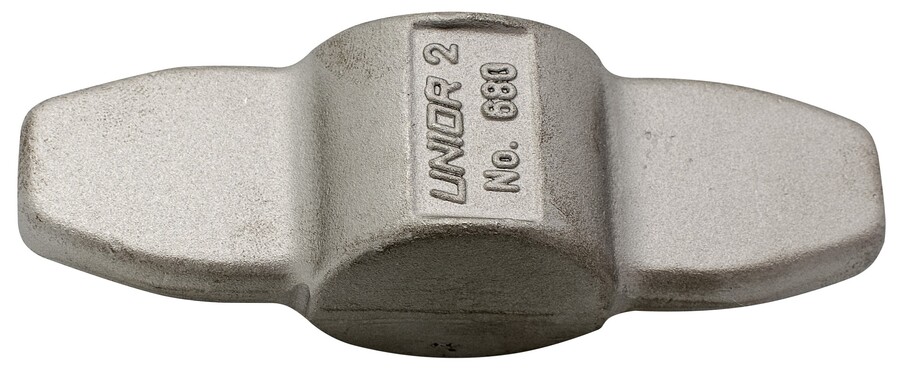
CNC working
a CNC machine is used to accurately work the head of the puller, which ensures smooth movement of the small handles.
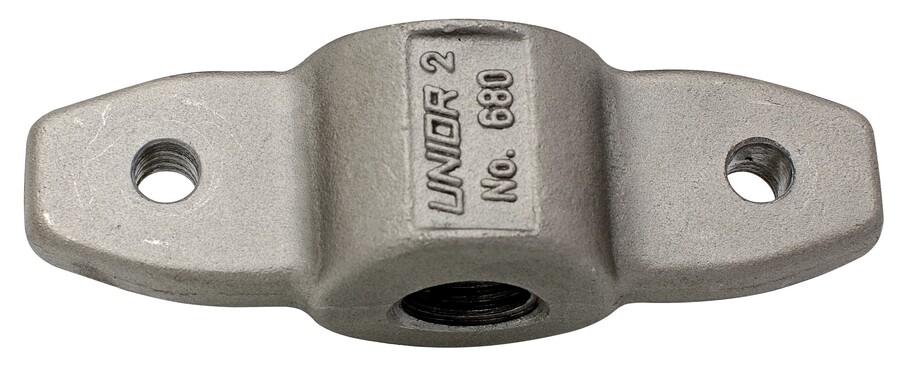
Heat treatment (quenching and tempering) and sanding
the heat treatment with hardening and tempering is intended to improve the structure of the steel, to provide greater hardness and toughness of the product and other properties required to overcome the strain that work with such products requires.
Chroming
the handle of the puller is plated with a thin, hard coating of chromium oxide, which protects against corrosion and wear and other mechanical damage. At the same time, it gives the entire Unior puller a glossy appearance.
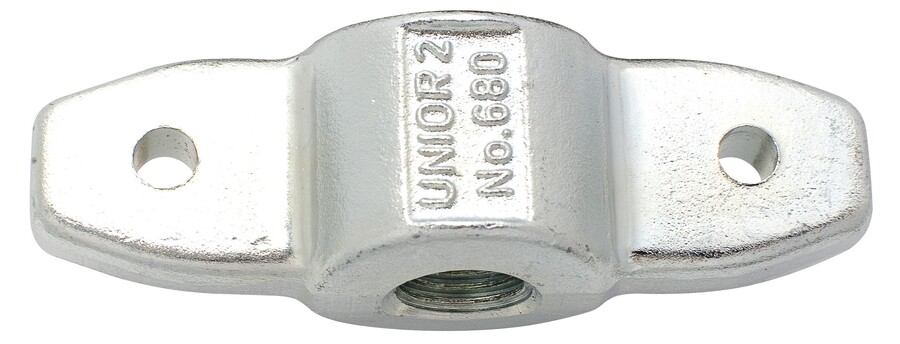
SPINDLE
Forging part
the forging part is made by warm upsetting, which provides the shape of the spindle head

CNC working
the CNC machine is used to accurately work the spindle that is the basis for thread rolling.
Thread rolling
is carried out on a special machine with special rollers. The resulting trapezoid thread is intended for use under greater strain.

Heat treatment (quenching and tempering) and sanding
Heat treatment with annealing and tempering is intended to enhance the structure of steel, product strength and toughness, and other properties required to withstand the loads to which such a product is exposed to. Sanding is used to clean the surface for further operations.
Burnishing and oiling
Burnishing gives a spindle a proper professional appearance and, together with the right oil, the necessary surface protection.

SMALL HANDLE
Forging and trimming a small handle
A forged part is made using drop forging technology. Drop forging provides various ergonomic product shapes. Suitable forging procedures maintain appropriate fiber orientation, leaving it the same as in rolled blanks. Superfluous material around a forged part is removed using a special-purpose trimming tool; material is trimmed to the desired shape, always making the weight of trimmings as low as possible.
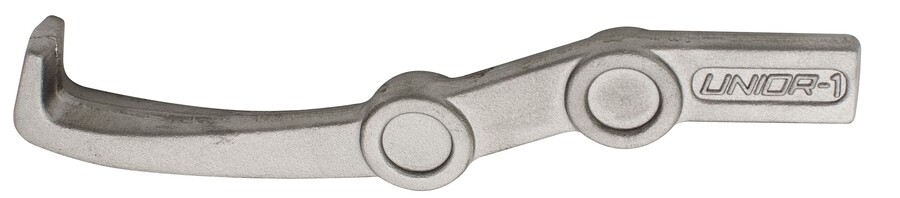
Hole broaching and CNC treatment
Broaching shapes the tip of the jaw. The latter must have optimal thickness for the necessary functionality of the broach. That is followed by CNC treatment of small handles that provides the necessary positioning of the broach assembly.
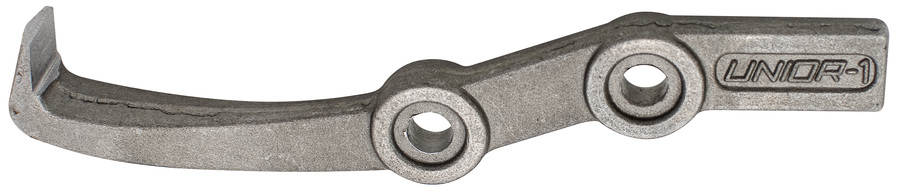
Heat treatment (quenching and tempering) and sanding
Heat treatment with annealing and tempering is intended to enhance the structure of steel, product strength and toughness, and other properties required to withstand the loads to which such a product is exposed to. Sanding is used to clean the surface for further operations.
Chroming
the handle of the puller is plated with a thin, hard coating of chromium oxide, which protects against corrosion and wear and other mechanical damage. At the same time, it gives the entire Unior puller a glossy appearance.
ASSEMBLY
Final assembly
the trained, skilled and meticulous workers performing the final assembly assemble the product into a solid whole that ensures the functioning and high quality of the Unior puller.
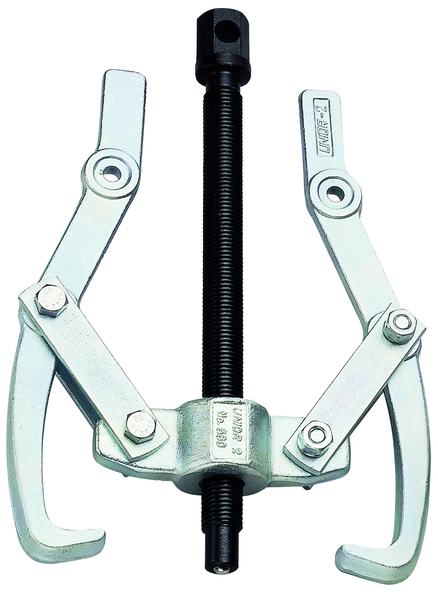