Hammers, punches and chisels
A special procedure for the manufacture of hammers
HAMMER
Cutting
Cutting material is the first operation in the technological procedure of wrench manufacturing. Optimum design of a cut provides optimal use of material.
Forging
Forging technology at Unior ensures excellent strength characteristics of wrenches. Notably, it maintains appropriate fiber orientation in a forged part, leaving it uninterrupted and the same as in a rolled blank. That characteristic of forged parts is vital for achieving the characteristics of products exposed to heavy and dynamic loads.
Trimming
Superfluous material around a forged part is removed using a special-purpose trimming tool; material is trimmed to the desired shape, always making the weight of trimmings as low as possible.
Broaching
The appropriate size of the hammer is achieved by broaching.
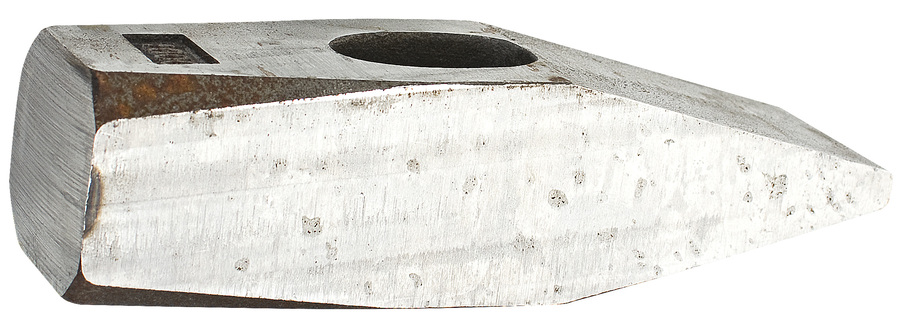
Induction hardening
Local heating and tempering of a hammer on the impact surface ensures a high degree of hardness for the functional part of Unior hammers. Annealing provides optimum microstructure and necessary hardness on impact surfaces. That ensures a long service life of hammers.
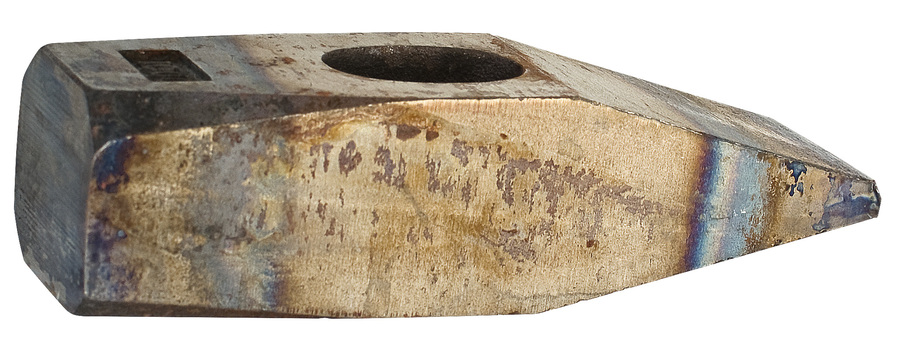
Coating
the surface is protected by electrostatic coating.
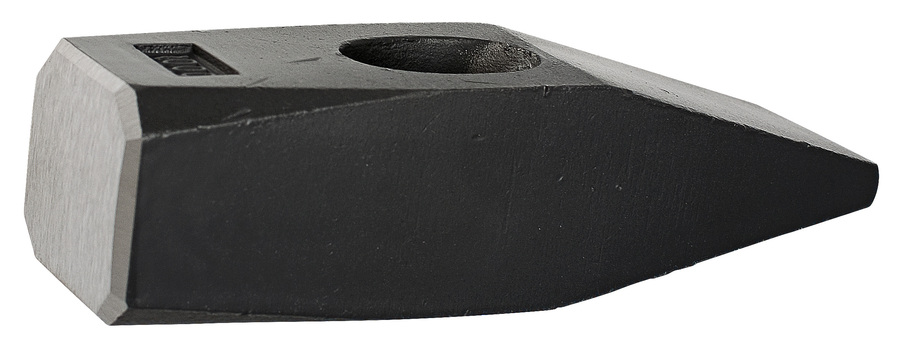
HANDLE
The handle is made using selected ash tree wood with the required characteristics in accordance with the DIN 68340 standard. It is protected with wax.
Marking of a handle
Making the blue inscription, which also reminds the user to handle the hammer correctly.
ASSEMBLY
Final assembly
The trained, skilled and meticulous workers performing the final assembly will assemble the product into a solid whole that ensures the functioning and high quality of the Unior hammers.
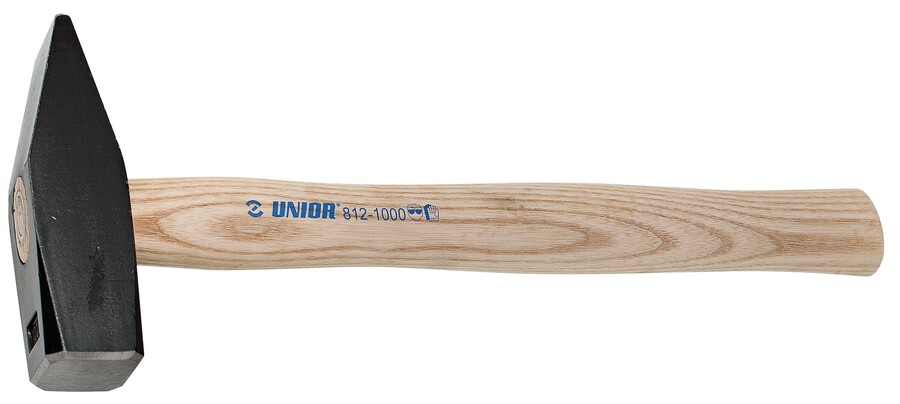